The LigerBots have had a productive week three week of robot build season! We made many advances in constructing our robot’s mechanisms, its electrical system, its software, and the wooden field elements we will use for driving practice. Many dedicated team members worked to better the robot and work out flaws in the design. Our FIRST awards group has also been making good progress on our Chairman’s and Entrepreneurship award submissions to FIRST.

We had a mid-build shop safety refresher from field elements mentor Jay, who made a model hand out of wood and vividly demonstrated the various ways students could hurt themselves if they were not alert when using the power tools. Then he taught our team how to better protect ourselves from losing fingers and eyes.

After much CADing and work on our milling machines, our chassis is finished, and our electrical group has finished wiring the drive train and mounting the motor controllers.

We decided to go with a tank drive that uses six wheels. The four rear wheels can roll only backward and forward. However, the front two wheels are omni wheels, which look like a string of beads wrapped tightly around a circular hub. An entire omni wheel can roll forward or backwards while its beads roll at 90 degrees to help the wheel slip sideways. As a result, the robot can pivot around its center to change directions. We hope this will allow our robot to be both nimble and difficult to push off course by defensive robots during competition.
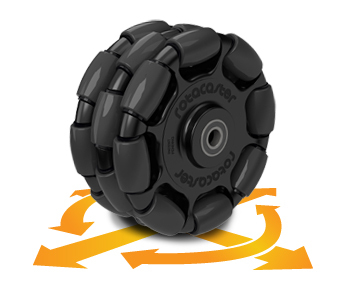
Our field elements group has created a frame and basket for the scale.
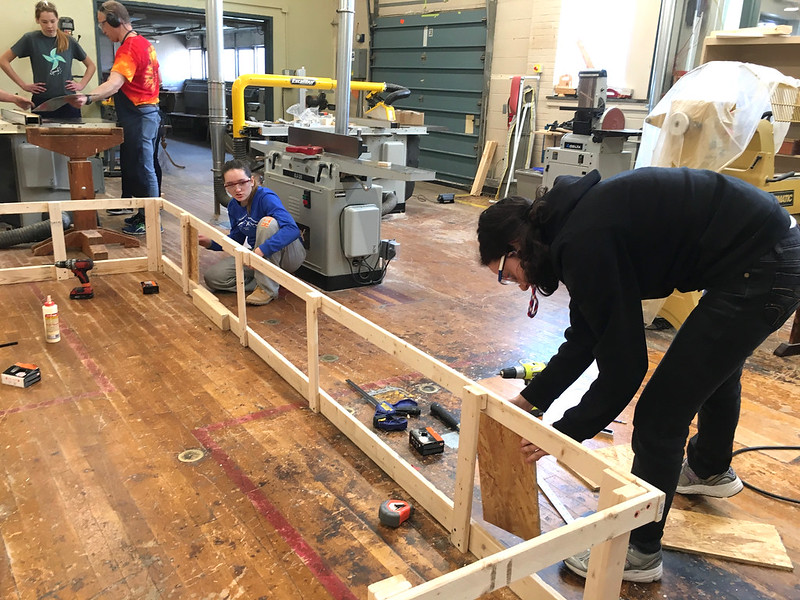
We have started adding the elevator mechanism to lift the “cube” game pieces, and are working on our fourth design for a cube intake mechanism.


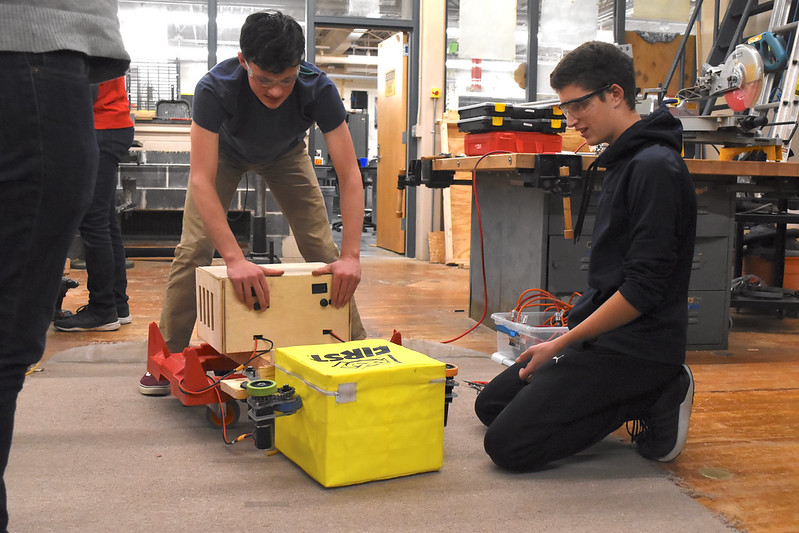
We started out using many wheels to suck in the cube and are now down to two. It takes a lot of time and concentration to keep designing and making improved mechanisms, but this iterative process is at the core of our team’s lessons in real-life engineering.